RFG – This creates a load bearing substrate. It insulates and forms a capillary break. It is also a sustainable material made of a waste product.
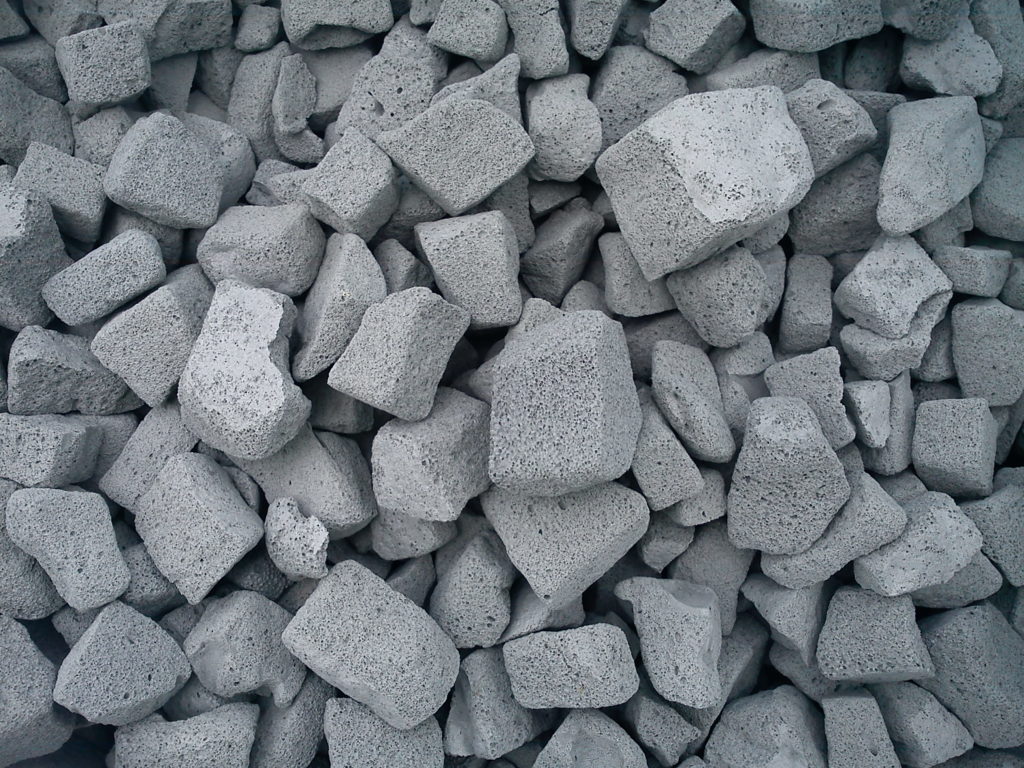
Geotextile Membrane – This separates the substrate and limecrete from the insulation layer.
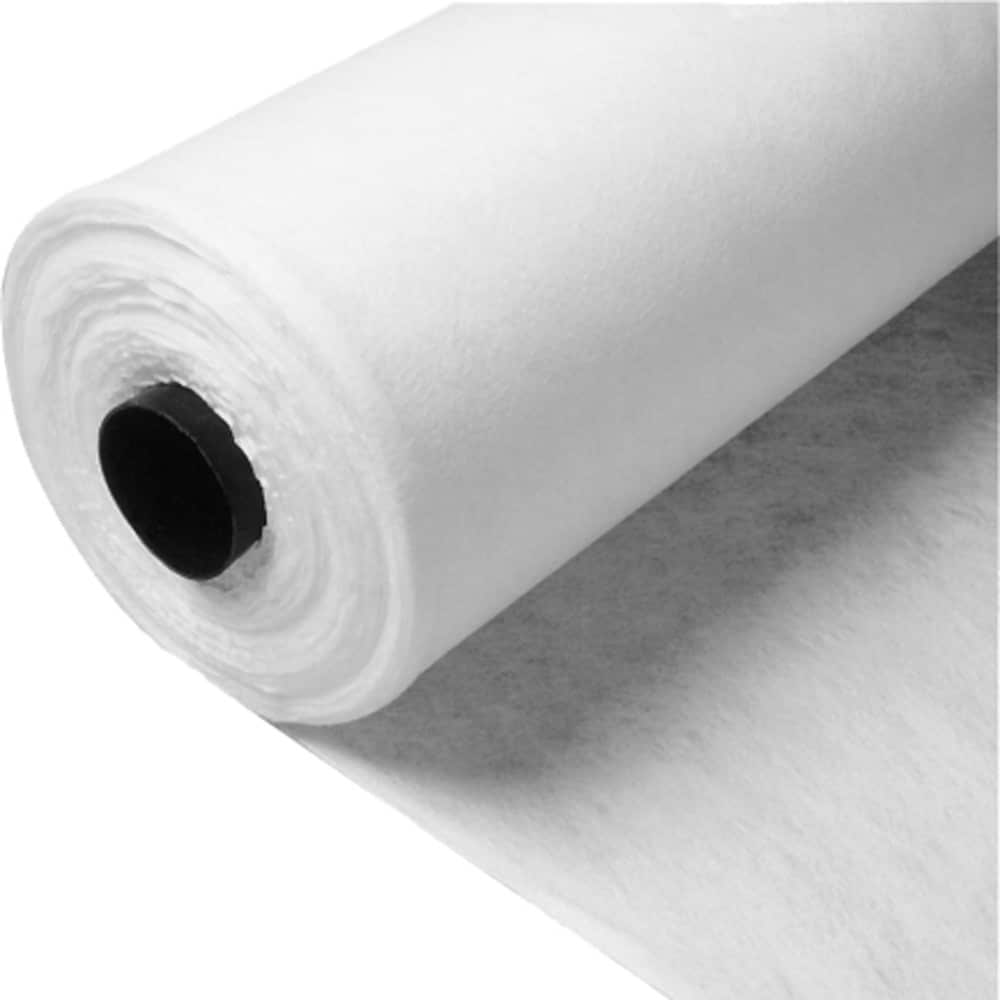
Aggregate – Depending on the requirement this would generally be a sharp sand or 0-15mm pumice.
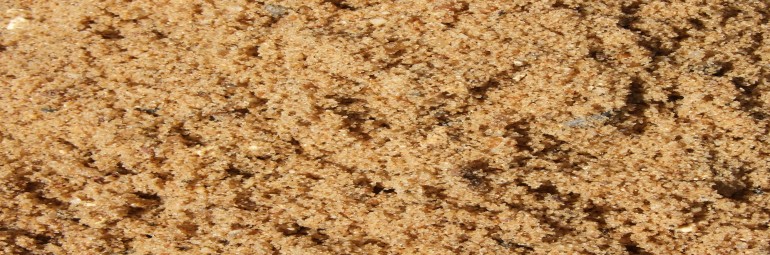
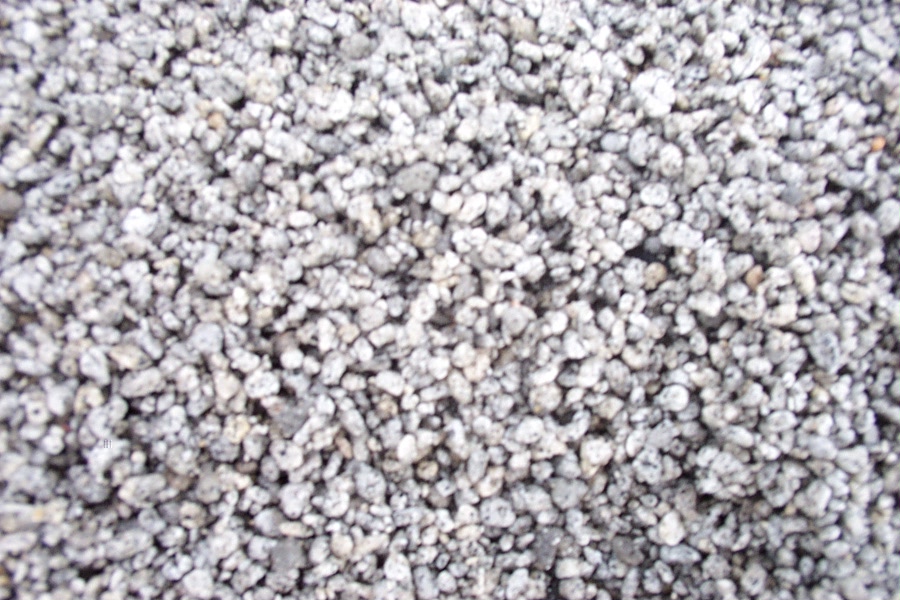
Geogrid – When using UFH this provides a grid for the pipework to be attached to.
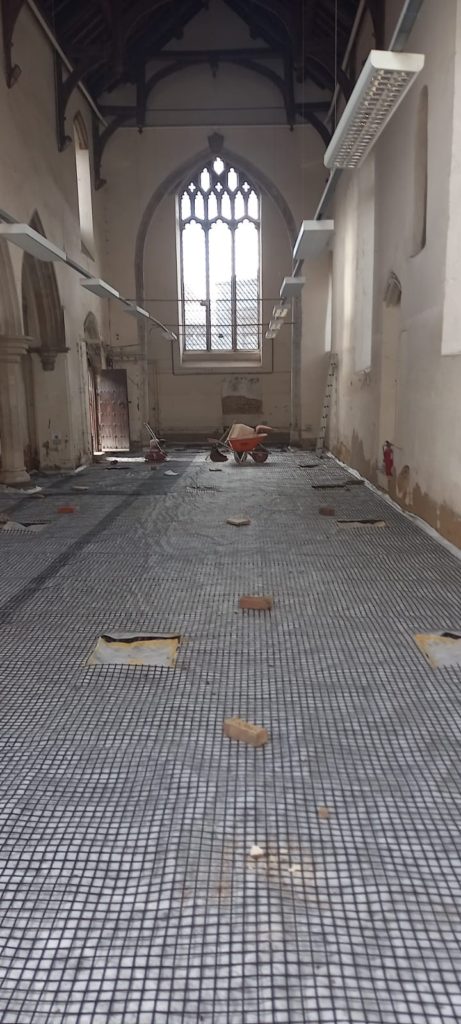
Fibres – 6mm polypropylene fibres help to increase the strength of the limecrete and decrease cracking.
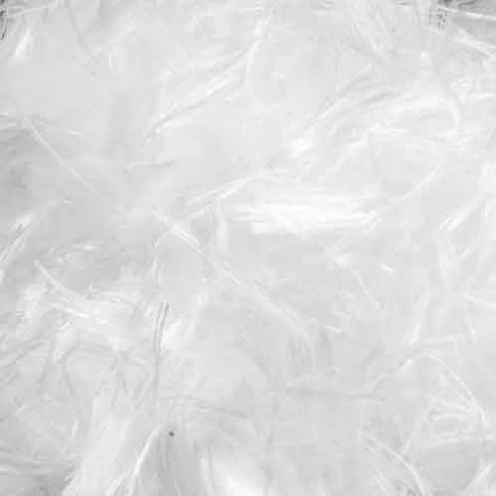
Cork or Foam Edge – This essential detail separates the wall from the limecrete, ensuring no thermal bridge and that both have their own independent moisture vapour transfer.
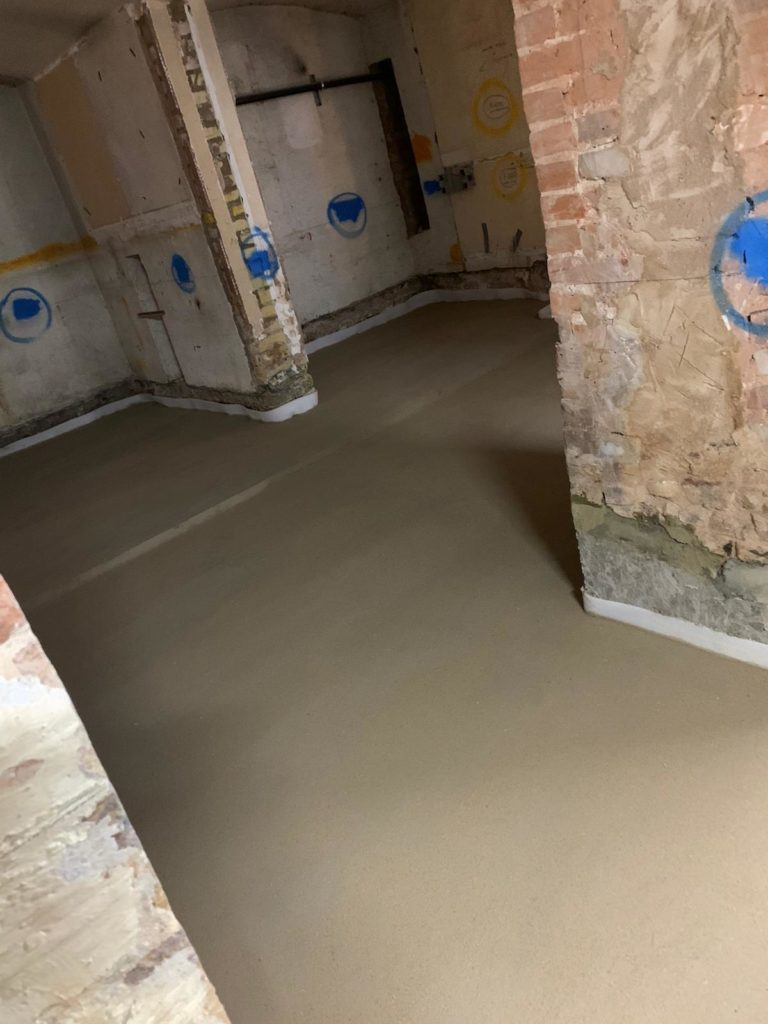
Water – As the lime we use is NHL5, the addition of water initiates the hydraulic set. Limecrete is ready for light footfall after 72 hours.
Lime – We use NHL5, the strongest of the natural hydraulic limes, which ensures the strength that is required for ground bearing slab is created.
Volumetric mixer – Mixes Limecrete with consistency, speed and efficiency.
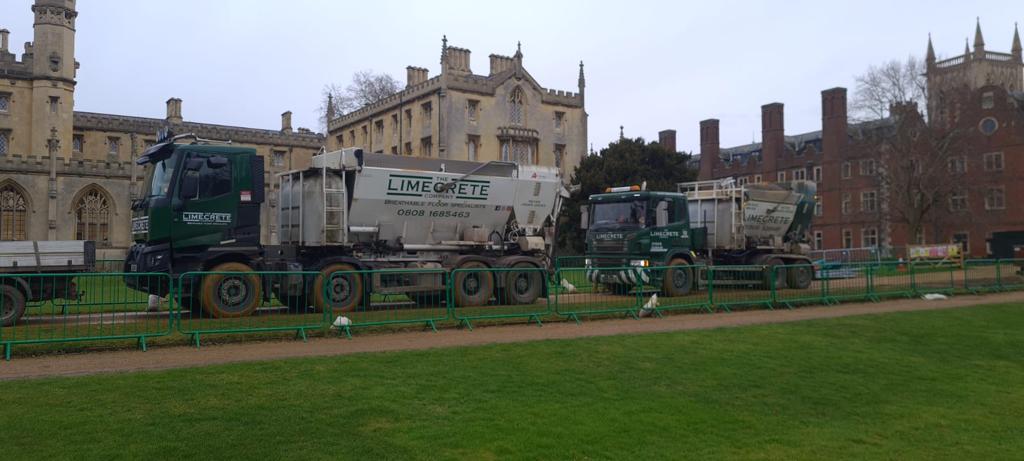
Our fantastic team 💖 – Hardworking, passionate and highly regarded!